A method to reduce the refrigeration load on a typical supermarket in hotter climates
The combination of HY-SAVE technologies, including Liquid Pressure Amplification (LPA), and compressor discharge heat reclaim & disposal can lead to significant improvements in refrigeration efficiency, especially in hot climates. These technologies work together to enhance the performance of refrigeration systems by ensuring optimal refrigerant flow and utilizing waste heat effectively.
The compressor discharge heat reclaim upgrade captures waste heat from the compressor discharge which can be a larger proportion of the THR by the condenser improving the system’s efficiency substantially.
In hot geographical locations, where cooling demands are higher, these technologies can help reduce the energy consumption of refrigeration systems, which is a major contributor to overall electricity usage. By improving the efficiency of these systems, supermarkets and other food retailers can significantly lower their operational costs and carbon footprint, contributing to a more sustainable future.
As a result, the system’s refrigeration efficiency can improve by 15 to 25%, which is a substantial increase, particularly in systems that have been operating inefficiently or have limited condensing duty. This upgrade not only reduces energy consumption but also extends the lifespan of the equipment by reducing wear and tear on the compressor and other components.
In summary, the LPA® pump is a valuable addition to refrigeration systems, especially in scenarios where the design has led to inefficiencies that can be rectified by installing a LPA pump. It’s an effective solution for achieving energy efficiency and sustainability in the refrigeration industry.
The LPA liquid refrigerant pump range has a remarkable track record, having been operational in commercial and industrial settings for over 40 years. This longevity is a testament to the durability and reliability of the technology. With a lifetime performance exceeding 25 years, these pumps represent a long-term investment that can deliver consistent efficiency and energy savings over decades.
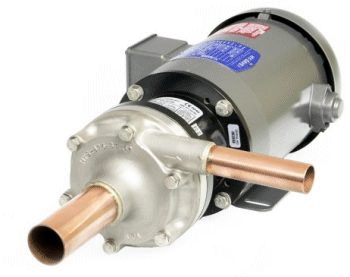

Such performance metrics highlight the pumps’ ability to withstand the rigors of continuous use while maintaining their effectiveness in improving refrigeration systems’ efficiency. This durability also means that the pumps contribute to sustainability efforts by reducing the need for frequent replacements and maintenance, further emphasizing their role in promoting environmentally friendly practices in the refrigeration industry.
hysave research development forecast 2025/2026
HY-SAVE’s commitment to research and development in the field of energy-efficient refrigeration design and operation has had a significant impact on reducing carbon emissions. Their advancements in system performance are not only enhancing efficiency but also contributing to substantial environmental benefits. The collective savings of over 320 million tons of CO2 is a remarkable achievement.
Looking ahead, the projection of reducing carbon emissions to around 500 million tons annually by 2030 is an ambitious and commendable goal. This reflects the potential of HY-SAVE’s technologies to make a considerable difference in the fight against climate change by reducing the carbon footprint of refrigeration systems worldwide.
Such projections underscore the importance of continuous innovation and the adoption of energy-saving technologies in mitigating the effects of global warming. HY-SAVE’s efforts demonstrate how industry-specific advancements can contribute to broader environmental goals and highlight the role of efficient refrigeration design in achieving a more sustainable future.
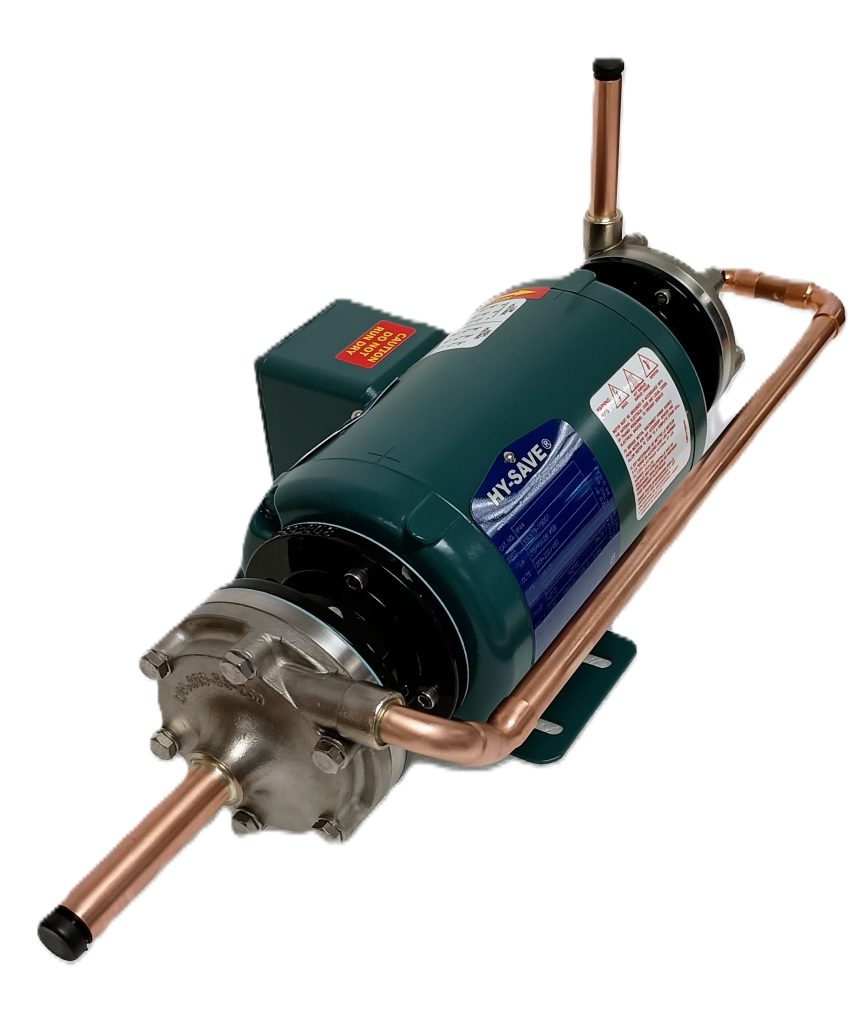
In January 2025, advancements in CO2 trans-critical circuits have led to a reconfiguration of system circuits to operate without liquid receivers. This development allows for a smaller overall package footprint, enabling higher tonnage per square foot for various applications, whether it be in the industry, commercial, or residential sectors. The elimination of liquid receivers simplifies the system design and can potentially reduce installation and maintenance costs while improving system efficiency. This is particularly beneficial in space-constrained environments where maximizing the use of available area is crucial. The ability to achieve higher cooling capacities in a compact space aligns with the ongoing trend towards more efficient and sustainable refrigeration solutions.